Prior to the design of a CoolTool mold insert, predictive engineering models are created based on the geometry of the injection mold tool and associative part being molded. These models are then analyzed by our design team, allowing for the identification of critical features. The identification of such features guides the design of conformal cooling lines within the mold design.
For example, the client first submits the CAD of their proposed part geometry or their existing mold insert, depending if the CoolTool being designed is a new tool construct or retrofit. Utilizing this information provided by the client and our injection mold design team, heat transfer models of the injection molding process can be developed utilizing our proprietary CoolTool algorithm. These models are analyzed by CoolTool designers to determine which areas of the injection are considered “hot spots.” Hot spots are regions of a plastic injection that are subject to larger thermal masses and extended cooling times.
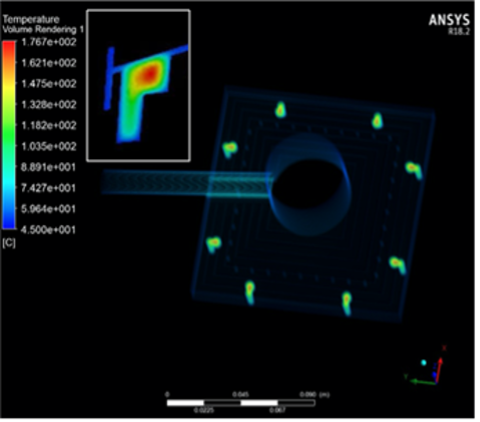
Upon identifying these hot spots, the design team is able to proceed, by first removing as much material as mechanically possible from these regions. The amount of material removed from these regions is determined by the design intention of the part, in some instances, the design of the part must be left completely unchanged.
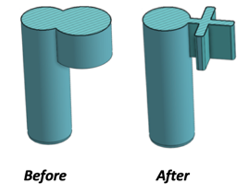
Following this, cooling channels are then incorporated into the new insert based on the design freedom enable through 3d metal printing. The placement of these channels is determined by the location of the hot spots, and cooling channels are placed within proximity of these regions. Lattice matrices are then designed into the cooling lines to maximize heat transfer.
After the design of these cooling channels, another predictive thermal model of the injection molding process is developed, this time accounting for the design changes of the CoolTool mold insert and associative molded part. The results of this subsequent model incorporate the effects of the conformal cooling passages into its algorithm. As a result, hot spots that would have formed in the conformally cooled insert can be identified, and the cooling line design process can be repeated to target these otherwise unforeseeable hot spots. The predicted cooling time improvements of these models are also shared with the client, to confirm the margin of improvement.